proudly serving
the mid-south
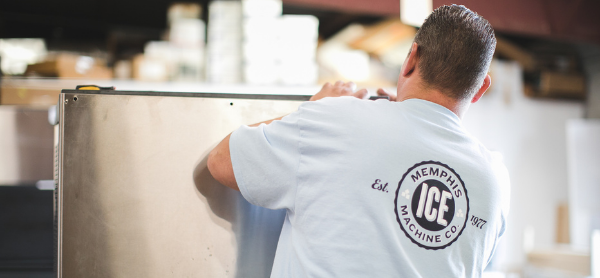
How to Extend Life of Your Ice Machine With Simple Maintenance Tips
When you’re running a business, your ice machine is one of those things you just expect to work—until it doesn’t. If you skip the upkeep, it wears down way faster, leading to costly repairs and headaches you probably don’t need. Honestly, the best way to extend the life of your ice machine is to stick to regular maintenance, clean it when you should, and use energy-saving settings so the parts aren’t always under stress.
Your machine has to work overtime during those steamy Memphis summers, so a good maintenance plan can help you avoid breakdowns right when you need ice the most. Here at Memphis Ice, we’ve seen it all since 1977, and honestly, a simple upkeep routine can really protect your investment.
Cleaning and draining your ice machine and getting expert check-ups keeps things running year-round. This saves money and keeps your ice fresh and safe. Let’s look at some easy steps you can follow to help your ice machine last longer and run better.
Regular Cleaning and Sanitizing
If you want your ice machine to keep up, you’ve got to keep it clean. Use the right products and follow a step-by-step process. That way, your ice stays safe, your equipment stays healthy, and you avoid those surprise breakdowns.
Proper Cleaning Frequency
You should deep clean your commercial ice machine at least twice a year. If your place is super busy, every three months is smarter.
Besides deep cleaning, wipe down the outside and clean the ice dispenser chute every week—mold and bacteria love to hide there.
Regular cleaning keeps slime away, which is a common nuisance that messes with your machine and your ice. If you run a restaurant or hospital, sticking to this schedule is just part of keeping things safe and up to code.
Honestly, it’s easy to forget, so set reminders or schedule maintenance so it doesn’t fall through the cracks.
Recommended Cleaning Solutions
Always go for cleaners made specifically for ice machines. They’re designed to tackle mineral buildup and germs without wrecking your equipment.
Skip household cleaners or bleach—they can do more harm than good, and you don’t want weird residues in your ice.
Descalers remove lime deposits, and food-safe sanitizers are a must. Some cleaning kits come in tablet form, which makes the process less of a hassle.
Rinse everything really well after cleaning. Leftover chemicals can mess with the taste and safety of your ice.
If you’re not sure what to use, just ask your Memphis Ice expert—they’ll know what’s best for your machine.
Step-By-Step Cleaning Process
- Turn off and unplug the ice machine.
- Empty the bin and toss out all the ice.
- Take out removable parts—like the scoop, trays, and filters. Wash them with warm, soapy water.
- Apply cleaner or descaler as directed. Let it sit to break down buildup.
- Gently scrub inside surfaces with a soft brush, especially corners and water lines.
- Rinse every part really well to clear out cleaner and debris.
- Sanitize inside surfaces with a food-safe sanitizer. Let everything air dry before putting it back together.
- Plug it in and turn it back on. Throw out the first batch of ice after cleaning—just to be safe.
If you’re ever unsure, reach out to Memphis Ice for professional help. Sometimes it’s just easier that way.
Routine Maintenance Practices
Keeping your ice machine in shape isn’t rocket science, but it does mean staying on top of a few key things. Check water filters, inspect parts for wear, and keep an eye on how your machine makes ice. These steps help you dodge expensive downtime and keep your ice clean.
Checking Water Filters
Water filters catch minerals and junk that would otherwise clog up your machine. If you slack on changing filters, scale builds up, your machine suffers, and your ice gets weird.
Check filters every month or as the manufacturer suggests. If you notice less ice or odd tastes, your filter’s probably overdue for a change.
It’s worth using a good-quality filter that fits your machine. Memphis Ice recommends keeping spares on hand so you’re never stuck. Clean water means less hassle, plain and simple.
Inspecting Components for Wear
Gaskets, seals, and fans don’t last forever. If they go, you could end up with leaks, overheating, or airflow problems.
Check these parts every few months. Look for cracks, rust, or anything loose. Don’t forget electrical connections and belts.
Here’s a quick checklist:
- Inspect door seals for cracks
- Clean off buildup from fans and vents
- Tighten any loose screws or connections
- Swap out worn belts
Staying ahead of wear and tear keeps your ice machine reliable.
Testing Ice Production Cycles
Your machine runs through cycles to freeze and drop ice. If those cycles get weird, you’ll get less ice or the quality will drop. Testing production spots problems before they get out of hand.
Watch cycle times and output every week. Listen for odd noises or delays. If ice forms too slowly or doesn’t drop, call a tech.
Memphis Ice can help with routine checks if you’d rather not handle it. Keeping cycles smooth means you’ll always have ice when you need it.
Optimal Installation Environment
Where you put your ice machine—and the air around it—matters a lot. Avoid extreme temps, keep air moving, and block direct sunlight. These steps help your machine last longer.
Ideal Location and Ventilation
Pick a spot with plenty of air circulation. Good ventilation keeps heat from building up around the machine. Don’t cram it into a tight corner or wedge it between other appliances.
Never put your machine outside or in damp areas without climate control. Humidity and weather swings are bad news.
Keep vents and fans clear of dust and junk. Blocked vents force your machine to work harder, which shortens its life. Clean air filters regularly to keep things flowing.
Managing Ambient Temperature
Ice machines like stable temps—usually between 50°F and 90°F. Too hot and you risk overheating; too cold and you get freezing issues.
If your space gets really hot or cold, try to keep the machine in a climate-controlled area. Memphis summers are brutal on ice machines without temperature control.
Preventing Direct Sunlight Exposure
Keep your machine out of direct sunlight. Sun heats up the surface, making it work harder and use more energy. That just wears things out faster.
If you can’t avoid a sunny spot, throw up a canopy or use an opaque cover. Even reflective paint on nearby walls can help cut down on heat.
Check the area now and then—trees and buildings shift or grow, and suddenly your machine’s in the sun when it wasn’t before.
Water Quality Management
Taking care of the water that feeds your ice machine is huge. Clean, filtered water means less damage and better ice—plus fewer surprises.
Importance of Water Filtration
A water filter keeps dirt, minerals, and chemicals out of your machine. Without it, parts clog or corrode, and you end up with expensive repairs.
A good filter also makes your ice taste and look better. Check and replace filters regularly to keep things moving. Memphis Ice suggests you change them based on your local water quality—just set a schedule and stick to it. It’s a small step that saves you from bigger headaches.
Monitoring Mineral Build-Up
Mineral build-up (scale) happens when hard water leaves deposits inside your machine. Over time, it slows down production and wrecks parts like the evaporator.
Watch for white or chalky deposits in water lines or on components. Clean them regularly with descaler to avoid long-term damage. If you ignore scale, you’re asking for breakdowns and bad ice.
Test your water and do routine cleanings. Staying on top of this helps you avoid nasty surprises.
Addressing Common Operational Issues
Spotting problems early is the best way to protect your ice machine. A little attention now saves you from big repairs later.
Identifying Warning Signs
Your ice machine usually gives you hints before it quits. Watch for slow production or ice that melts too fast. That’s usually a temperature or water flow issue.
Taste and smell matter, too. Weird flavors or odors can mean buildup or dirty water lines.
Leaks or frequent shutdowns are red flags. If you ignore them, you could end up with compressor damage or scale buildup—expensive stuff.
Catching these signs early means you can call for maintenance before things get out of hand. Memphis Ice helps businesses spot problems before they become disasters.
Responding to Unusual Noises
If your ice machine starts making weird sounds, pay attention. Clicking, grinding, or hissing usually means parts are wearing out or water lines are blocked.
A buzzing compressor could mean it’s struggling—maybe because parts are dirty or starting to fail. Jumping on noises quickly keeps things from getting worse.
Regular cleaning and inspections help, but if you hear something off, schedule a service check. The Memphis Ice team can find and fix problems before they mess up your day.
Seasonal Upkeep Tips
The time of year really does matter. Taking a few extra steps before busy seasons or power hiccups can keep your machine running and save you money.
Preparation for High Usage Periods
Before the rush—like summer—give your ice machine a good once-over. Clean inside and out to clear out mineral deposits and debris. Swap out old filters to keep the water clean and your ice top-notch.
Make sure the machine sits in a cool, breezy spot. Hot temps make it work harder, so keep it away from heat sources and sunlight. If it’s outside, move it indoors or at least into a climate-controlled area until things slow down.
Test your water supply and drains to avoid hiccups. Low pressure or clogged drains can shut you down when you need ice most. Schedule service or maintenance before peak season so you’re not scrambling last minute.
Protecting Against Power Fluctuations
Power surges and outages can fry your ice machine’s electrical parts in no time. To help prevent that, grab a surge protector made for commercial gear. It soaks up excess voltage, saving you from headaches and expensive repairs later.
If blackouts are a regular thing in your area, it’s probably worth looking into a backup power source. Even a quick flicker can make your ice machine reset or glitch out. Pop in an uninterruptible power supply (UPS), and your machine keeps chugging along during those short outages—definitely a relief if you rely on steady ice.
Don’t forget about the basics: keep those electrical connections tight and clean. Corroded or loose wires? They’re just asking for trouble. Have a pro check your setup now and then to catch any weirdness early. Your ice machine works hard, so it deserves reliable power—give it some love, and it’ll keep the cubes coming.
When to Seek Professional Service
Sometimes, you just need to call in the experts. If your ice machine starts acting weird—odd noises, less ice, or the ice looks off—it’s time for professional help.
If the machine keeps shutting down, or you spot leaks or puddles, don’t ignore it. Letting these issues slide can turn a small fix into a big, expensive mess.
A lot of businesses get their machines checked out by a pro twice a year, sometimes more if things get busy or the environment’s rough. Frankly, it’s just smart to stay ahead of problems.
At Memphis Ice, we always say—reach out before something small snowballs. We’ll figure out what’s wrong and get you squared away fast, so you don’t get stuck without ice when you need it.
Here’s a quick checklist for when to call in the pros:
- Weird noises or shaking
- Not enough ice, or it melts too fast
- Leaks or puddles you can’t explain
- Warning lights or cryptic error codes
- Funky smells coming from the machine or ice
Don’t wait for the rush to get your machine serviced. Get in touch with Memphis Ice early and keep things running smooth when it matters most.
Frequently Asked Questions
Keeping your ice machine clean, watching the temperature, and sticking to a good maintenance routine all help it run better and last longer. The right water filter makes a big difference, too. And if you know how to spot and fix common problems, you’ll dodge most big breakdowns. Don’t forget—storing your ice right keeps it fresh and safe.
What’s the best way to clean your ice machine regularly?
Aim to clean your ice machine every month or two, maybe three, depending on how much you use it. Focus on the inside—the bin, water filter, and drip tray. Grab a food-safe cleaner and stick to what the manufacturer says.
For a deeper clean, don’t skip the condenser and evaporator. It keeps everything humming along.
Can you share some tips for maintaining optimal operating temperatures for my ice machine?
Keep your ice machine where it’s cool, ideally between 50°F and 90°F. Don’t put it near ovens or in the sun—heat just makes it work too hard.
Check the condenser fan and coils now and then. If they’re dusty or blocked, your machine’s gonna struggle to keep up. A steady, cool spot helps a ton.
What are the recommended maintenance routines for an ice machine?
Have a pro give your machine a once-over at least twice a year. They’ll check the electrical stuff, water lines, and moving parts.
Regular cleaning and jumping on repairs quickly will save you from bigger headaches. Memphis Ice has maintenance plans if you want to keep things simple and stress-free.
Could you advise on the type of water filtration system to use with an ice machine?
A solid water filtration system cuts down on minerals and gunk that can mess with taste or cause scale. Go for a commercial-grade filter built for ice machines, and make sure it matches your water’s hardness.
Swap out those filters on schedule. It’s the best way to keep your ice tasting good and your machine running right.
How can I troubleshoot common issues with my ice machine to avoid breakdowns?
If your ice machine slows down or stops making ice, first check the water supply and temperature. Look for clogged filters or dirty parts. Weird noises? Might be a fan or compressor issue.
If you see leaks, error codes, or problems that won’t quit, call a Memphis Ice tech. Fixing things early always beats waiting until it’s urgent.
What’s the proper way to store ice from an ice machine to maintain its quality?
Honestly, ice does better when you stash it in a clean, dry container—preferably one that’s not sitting next to something with a strong smell. You really don’t want your ice picking up weird flavors from last night’s leftovers. Always use a scoop, not your hands. It’s just more hygienic.
Cover the ice bin, too. If you leave it open, the ice gets exposed to air, and then it starts clumping or melting in odd ways. Nobody wants that.
Recent News
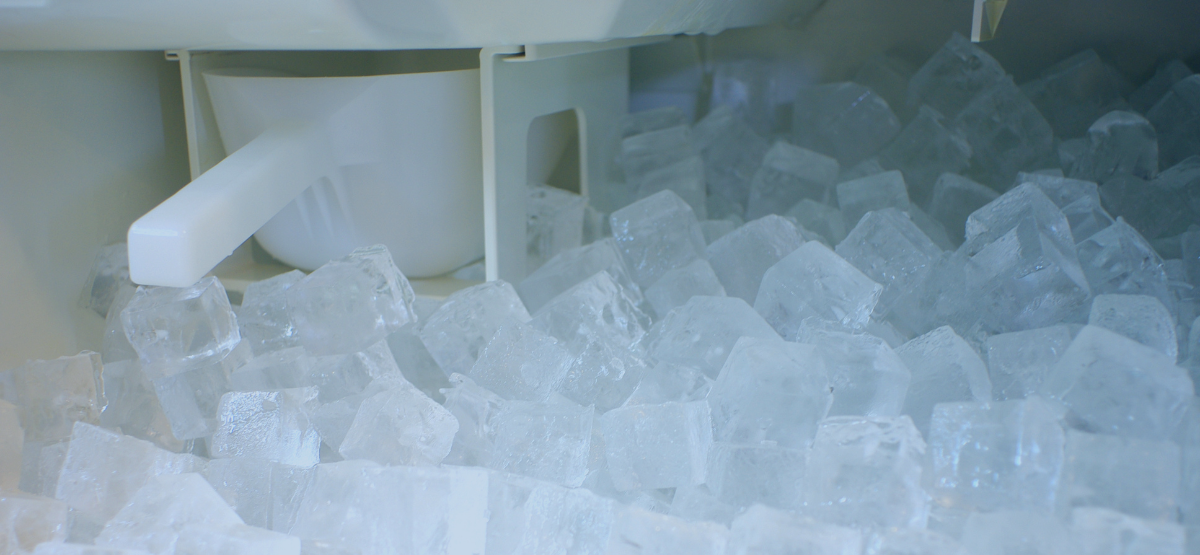
Commercial Prep Table Maintenance Tips for a Cleaner, Longer-Lasting Kitchen
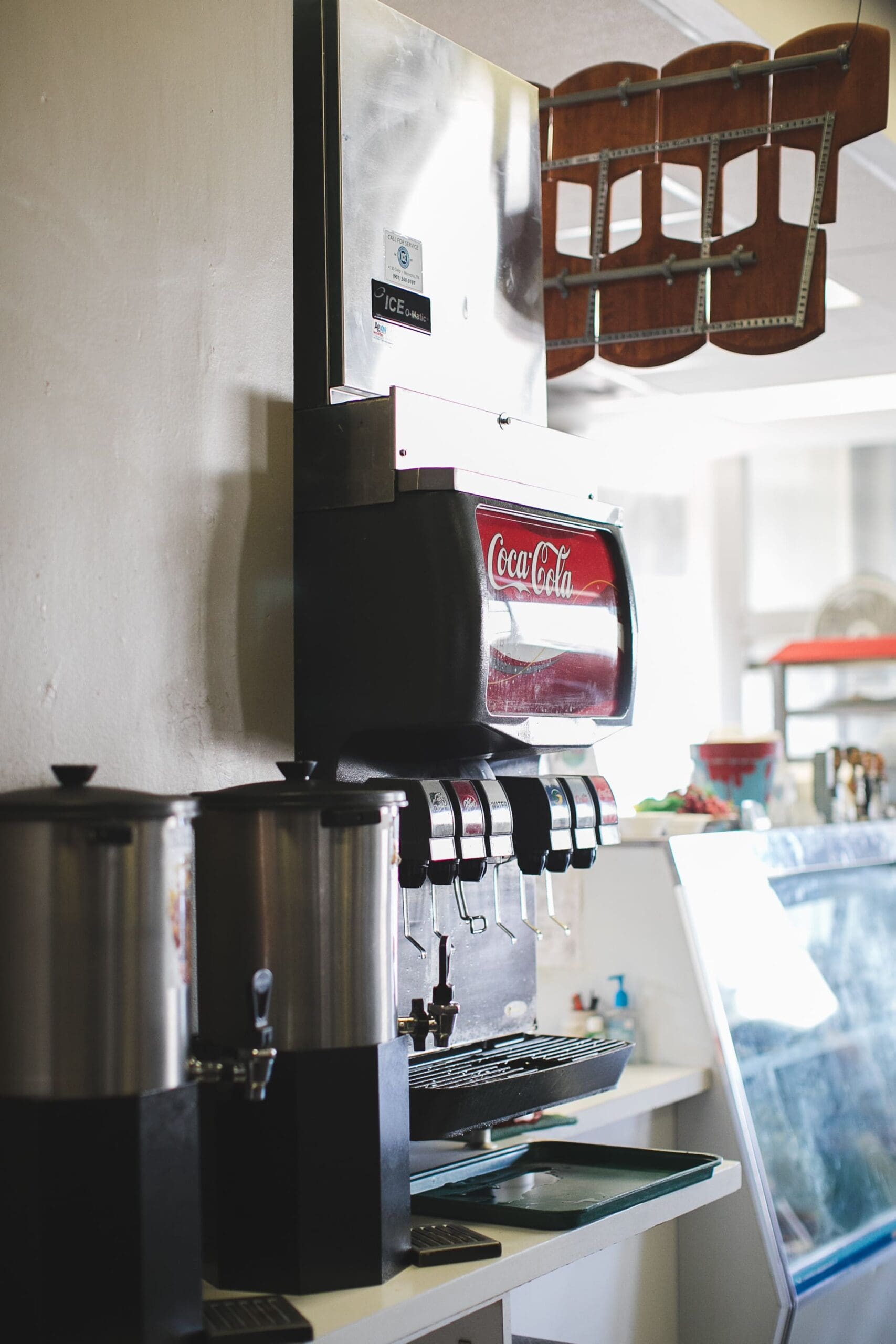
Commercial Ice Machine Rental Made Easy for Your Business Needs
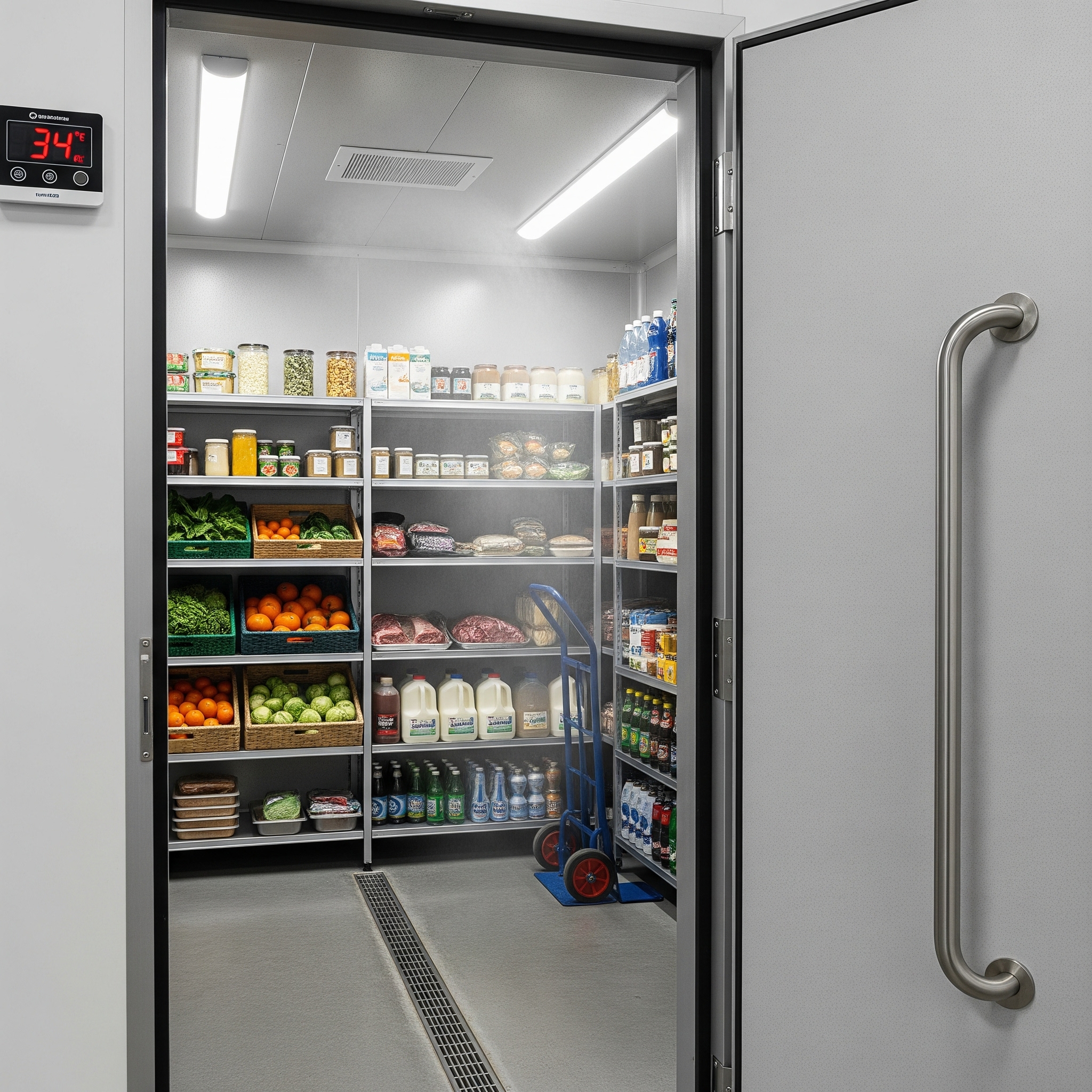
Walk-In Freezer Not Cooling Troubleshooting Tips and Fixes
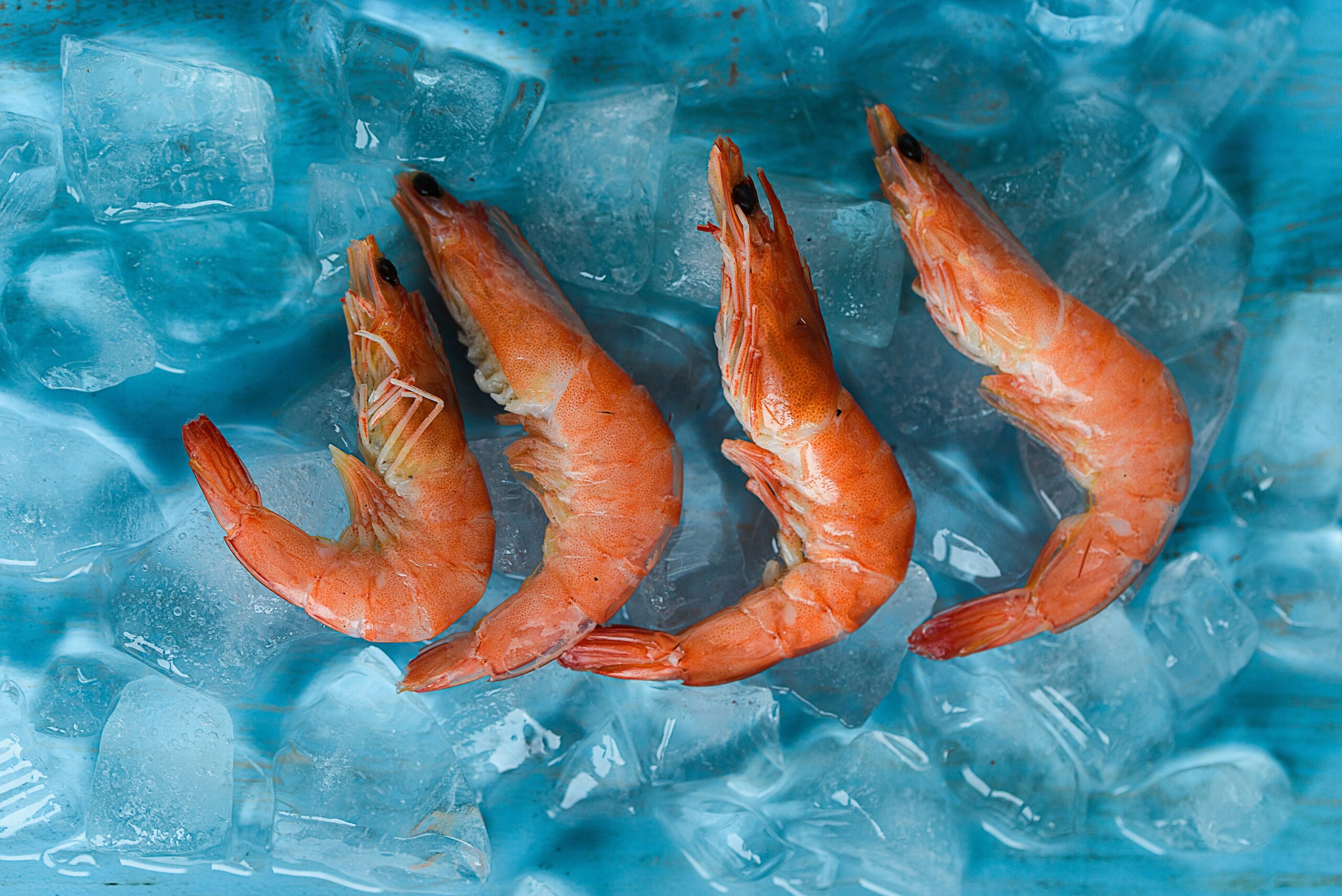
Mid-South Commercial Refrigeration Friendly Guide to Efficient Cooling Solutions
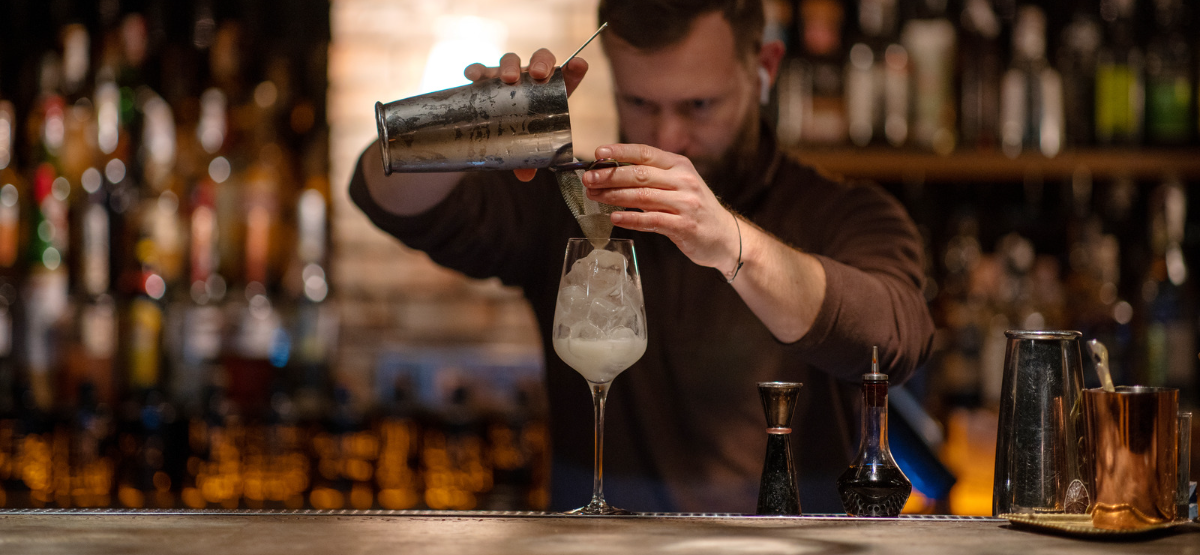