proudly serving
the mid-south
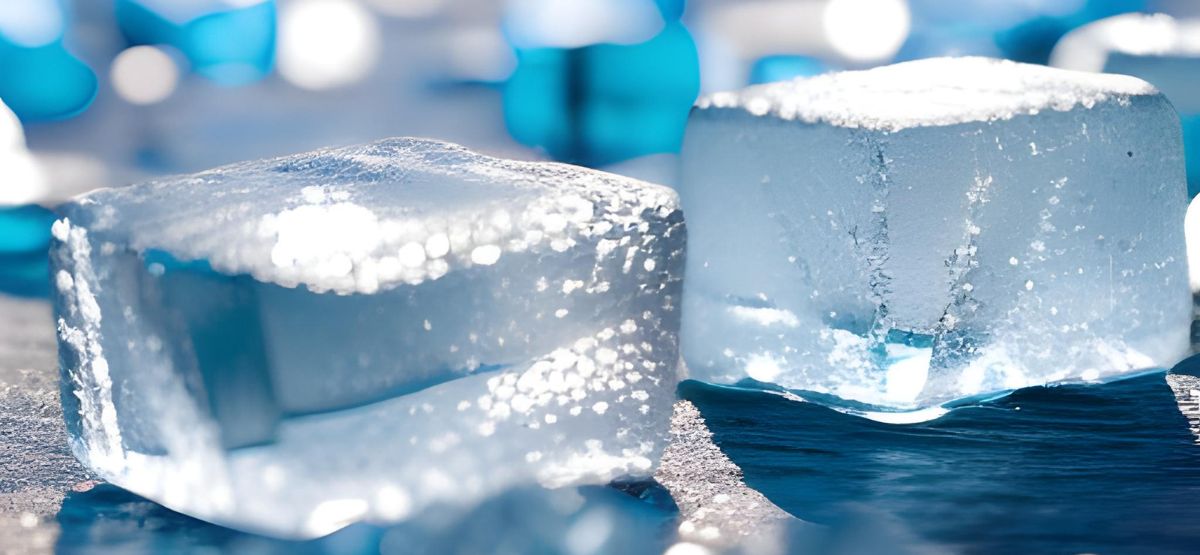
3 Common Problems with Commercial Ice Machines – Memphis Ice
Use these tips to avoid costly issues with commercial ice machines. Keep your machine running smoothly with installation and maintenance from Memphis Ice.
An ice machine is essential to most commercial kitchens. That’s why when your commercial ice machines break down, your business operations have a serious meltdown.
The good news is that you can take steps to avoid common problems with commercial ice machines. The other good news is that most of these problems are pretty easy to head off if you get an early start. So keep reading to find out 3 common ice machine issues and what you can do to prevent them.
3 Common Commercial Ice Machine Problems
1. Poor Water Filtration for Your Ice Machine
If you’re having problems with your ice machine, it could be because your water filtration system is not working properly—or maybe because you don’t have a filtration system at all. If you don’t have a water filtration system in place, stop right here and go get one.
Water filtration systems are a must for commercial ice machines. They remove impurities from hard water that would otherwise affect the quality of your ice, and lead to serious problems for your ice machine. Without a water filtration system, your ice machine’s internal components are exposed to damage, leading to costly repairs.”
- How Does Hard Water Damage An Ice Machine?
- Hard water is full of minerals like calcium and magnesium, causing serious buildup inside the components of your ice machine.
- When scale builds up on parts like inlet and water dump valves, it can prevent them from opening and closing the water dump valves and discarding water, which means your ice machine becomes a man-made lake. We’re talking flooding—serious flooding—inside your equipment and your ice machine will trip a “low water” error (which is ironic, because you’ve actually got a lot of water—just not where it needs to be).
- Hard water scale can build up at surprising speeds. And it won’t just affect your ice machine inlet and dump valves. Ice machine pumps, and ice thickness probes are also susceptible to hard water buildup, and they cause slower ice production, misshapen ice, or irregular ice harvesting.
- Make sure to get a good water filtration system designed specifically for your commercial ice machine, and make sure it can remove chlorine, sediment, and other impurities from the water. Proper filtration will extend the life of your machine, and prevent costly repairs.
2. Improper Commercial Ice Machine Installation
Installing an ice machine isn’t just a plug-it-in-and-forget-it process. There are several factors that go into installing your ice machine correctly that can affect the lifespan of your investment. We take commercial ice machine installation seriously—so seriously, in fact, that we devoted an entire blog post to the subject (so go check it out).
A few key takeaways include:
- Ensuring sufficient electrical output
- Installing your ice machine in an ideal location (away from extreme temperatures)
- Planning for excess water drainage
- Installing a main water shutoff valve within 6 feet of the ice machine
Ideally this would all be done when your ice machine was installed. But if the environment of your equipment isn’t optimal, it’s better to make the necessary changes now—before it’s too late.
3. Lack of Commercial Ice Machine Maintenance
Regular maintenance is a crucial step to ensuring your ice machine runs smoothly. We talk a lot about preventative maintenance here on The Scoop because it’s so important to the longevity of your commercial refrigeration equipment.
Without routine maintenance, mold, slime, hard water buildup, grease, and dust can accumulate inside your ice machine, gum up the mechanisms, and prevent proper air circulation. This puts undue strain on your machine.
“When the internal parts of your equipment are dirty, your ice machine has to work twice as hard to produce ice, which strains and eventually damages other parts.”
If you don’t have time to routinely clean and inspect your equipment, that doesn’t mean it can’t get done. You can hire a professional service technician to routinely clean and maintain your ice machine so you don’t have to worry about it. For our clients who have enrolled in our Preventative Maintenance Program , the peace of mind that comes with professional care means they can focus on running their business and not worry about surprise repair bills caused by a dirty ice machine.
Partner With The Best Ice Machine Service & Repair In Memphis
At Memphis Ice Machine Company, we know your ice machine is a critical part of your business. That’s why we work hard to ensure your commercial refrigeration equipment is installed correctly, maintained regularly, and ready to help you get the job done.
Our technicians are experts on leading ice machine brands like Ice-O-Matic, Manitowoc, Whirlpool, Frigidaire, KitchenAid, and more. When you call Memphis Ice, you can be sure you’re getting the best commercial appliance service and repair in the Memphis area. Contact us today to discuss your ice machine needs!